I. NEW CATEGORY
- Dyson Supersonic – Hairdryer
- Dyson Airwrap – Hair Styler
II. CONTINUOUS IMPROVEMENT – FLOORCARE
- Upright vacuum cleaner catch failure
- Upright clelanerhead motor nuisance / bearing issue / power draw
- Upright cleanerhead turbo gear issue
- Upright vacuum cleaner upright lock (Swivel) structural issue
III. RESEARCH AND DEVELOPMENT – FLOORCARE
- Dyson Small Ball (DC 50 Replacement)
- Dyson Ball Animal 2
- Cordless Floorcare product (ingress, separation system, sensors, structural)
- Dyson Slim DiIgital (structural optimization to make it lightweight and not to lose robustness )
- V11 accessories (Dok) – Patent in force: Application Number: GB2019053464; Publication Number: 2020/136366 – link
NEW CATEGORY
1. Dyson Supersonic – Hairdryer
Short Description: My first project at Dyson, I had to hit the ground running. It was pre transfer time for the project, few iterations left to the finish before it gets to South-East-Asia for final manufacturing adjustments – plenty of work, not much time. It was time of a lot of testing, fine tuning and de-risking some of the remaining concerns of high priority. At this stage the emphasis for me was to manage heat for the electronics in the product, make sure all electronic components are robust and safe based on FMEA risks. Final touch to the shape of the PCB.
Result: The Dyson Supersonic became success in the beauty market, stars, celebrities, hair professionals and ordinary people made the product to be quickly sold out in some places. It had unique look, was very efficient, safe to the hair and ergonomic – a game changer on the market.
2. Dyson Airwrap – Hair Styler
Short Description: This was the second product in the New Category to be commercialized and together with the Supersonic they created Beauty Category in Dyson. They were soon joined by the Dyson Coral – Hair Straightener. It was early stage of the project and I was involved in the heat mapping and distribution for a short time then jumped on the attachments section where the Coanda Effect is utilized for attaching the flow to the surface and create “automatic wrap”. This was the stage where changing direction of the flow was developed to allow symmetrical curl for the users. I was also involved in dust ingress research as this was new environment for Dyson Digital Motors to face (hair styling chemicals, wide range of hair from around the world population potentially reaching the motor) the test had to be recognized and set up, data had to be analyzed to make sure the robustness of the product is met. This was a study in parallel to serve the Supersonic final checks and complement previous studies. After defining testing rig to get first samples of the products in to the ingress testing I was given a task to analyze drying efficiency of the Airwrap for various hair types and compare this with the most efficient competitors. Testing, data crunching and making conclusions to generate standard testing procedure so when the product is more matured it will be utilized for validation. The test procedure would have to be scrutinized by Gauge R&R, like every other one in the company.
Result: Just like the Supersonic, great product that caught the attention by it’s looks, functionality, efficiency and unique hair styling feature that uses mass of discharged air to follow the curvature of the attachment and have enough energy to “grab” user’s hair for styling and drying.
II. CONTINUOUS IMPROVEMENT – FLOORCARE
1. Upright vacuum cleaner catch failure
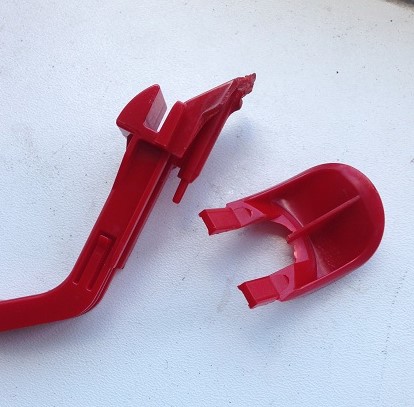
Short Description: One of the best-selling upright vacuum cleaners suffered with a breaking catch. Replacement involved sending expensive assembly as fitting of the broken part was too complicated for average user. My job was to find the root cause, provide solution, analyze and test the component so the product is robust enough and the failure rate is reduced without over engineering. It was quite complicated investigation as the component was part of an assembly mechanism consisting moving handle, spring, locking mechanism. Usage of the assembly was to carry the machine by the handle but when required the catch was supposed to release the bin to be emptied. FEA and testing of obvious case scenarios weren’t showing anticipated behavior. 5 Whys and Ishikawa diagram accompanied with additional scenarios testing has led to the answers which gave a light in to the root cause.
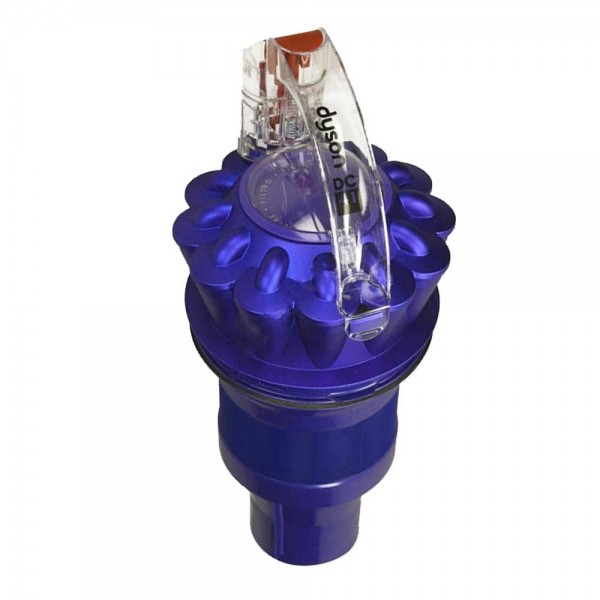
Result: Based on the findings, adjustments were applied to the targeted component and tests were repeated to confirm the change. It has also proven that in some cases prototyping material may be more displaced without breaking, making it more resistant than production material for such case scenario, and making the results misleading. My work had measurable impact on the money saving as the product was sold in millions worldwide and significant reduction of the failure rate improved product robustness and perceiving of the brand improvement.
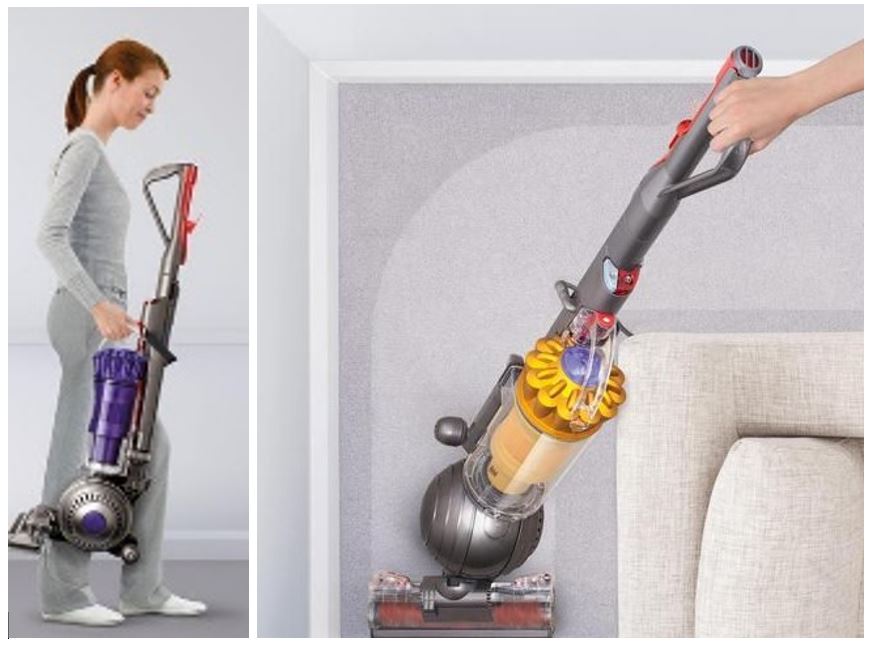
2. Upright clelanerhead motor nuisance / bearing issue / power draw
Short Description: A cleanerhead of one of the models had an issue with stalling that was recognized as priority to be investigated. Some of the results from the field has shown problems with bearing, some were having issue but bearing was still within the limits of resistance so another factor was taken in to consideration. This was the algorithm of the motor control that was too “sensitive” or vacuum generated in the cleanerhead was elevated so much that it created too much load on the brushbar. Analysis began to eliminate each of the factors, standard company tests were utilized to measure all the required parameters. I have also proposed new tests to analyze water ingress inside the brushbar to estimate risk of droplets travelling into the brushbar and their reach proximity to the bearing. The test has shown that the droplets wouldn’t penetrate deep enough to create a risk to the bearings, measured pressures and power draw was within the limits on various worst-case scenario surfaces. In the end the software was tested and algorithm altered to understand its impact on the performance.
Result: Finally, after all investigations, changes were applied and the fix was possible to be implemented without elevating the cost. Failure rate of the issue fell down to zero.
3. Upright cleanerhead turbo gear issue
Short Description: On some of the failed turboheads the transfer gears were found to have broken or grinded teeth. My task was to establish and propose a fix of the issue to reduce failure rate. Disassembled cleanerheads and gearboxes were analyzed in search for obvious root cause of the gears. Presence of dust and sand was observed so over torqueing was neglected. Ingres testing was applied on new assemblies, pressure mapping was done.
Result: Results were noted and conclusions were passed on South-East-Asian team to apply recommended changes. Fix was applied and the issue has reduced to zero.
4. Upright vacuum cleaner upright lock (Swivel) structural issue
Short Description: Customers complained at an upright vacuum cleaner not keeping the up-right position. Returned machines were shown with swivel component in the mechanism being broken. Based on FEA results, weak areas were highlighted and confirmed by tests.
Result: Results were noted and passed on South-East-Asian team to apply recommended changes. Fix was applied and the issue has reduced to zero.
III. RESEARCH AND DEVELOPMENT – FLOORCARE
1. Dyson Ball (DC 40 Replacement)
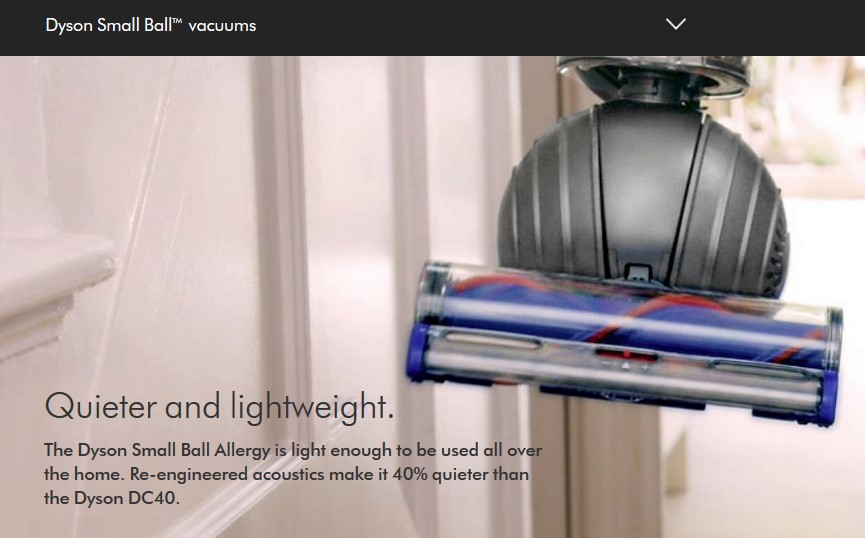
Short Description: This machine was a successor of the DC 40 and the main goal was to provide a product that will fulfill EU noise regulations.
Result: The machine is 40% quitter than the DC40! Its weight is 6,9 kg.
2. Dyson Small Ball Animal
Short Description: This machine was a successor of the DC 50 and the main goal was to provide a product to match EU noise regulations as with the Ball.
Result: The machine noise level was significantly reduced. It was also smaller by 30% than other Dyson up-rights, only 5,5kg.
3. Dyson Ball Animal 2
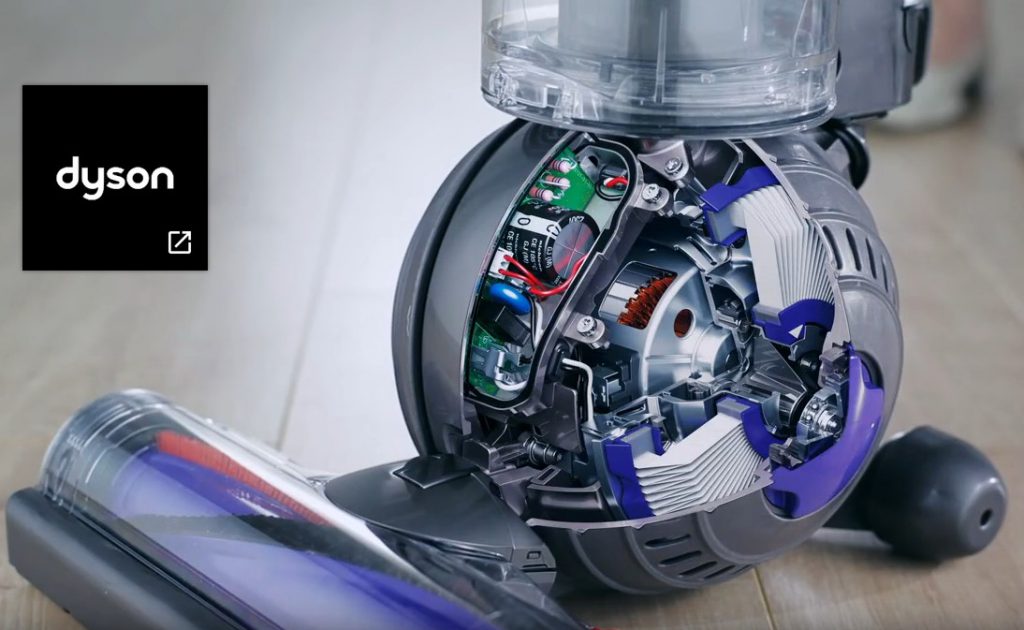
Short Description: Powerful suction and 7.34 kg were demanding parameters for the stiffens and structural robustness of the machine. These parameters have played crucial role in improving user comfort and perception.
Result: The machine improved its stiffness significantly by improving connections engagement. This made the machine much more ergonomic in handling considering its powerful suction and quite large mass.
4. Cordless floorcare product (structural optimization to make it lightweight and not to lose robustness [wand + mainbody])
Short Description: Dyson Digital Slim was considered be ergonomically adjusted for Chinese market. I have created concepts where I focused on reducing mass without losing robustness. Various improvements of manufacturing methods were considered e.g. aluminium extrusion as well as optimization of plastic connections, looming and electrical connections. The challenge was to pass all rigorous Dyson tests to meet the robustness specification.
Result: Released in Q2 of 2020 the product is 30% lighter and 20% smaller than it’s predecessor.
5. V11 accessories – V11 Dok
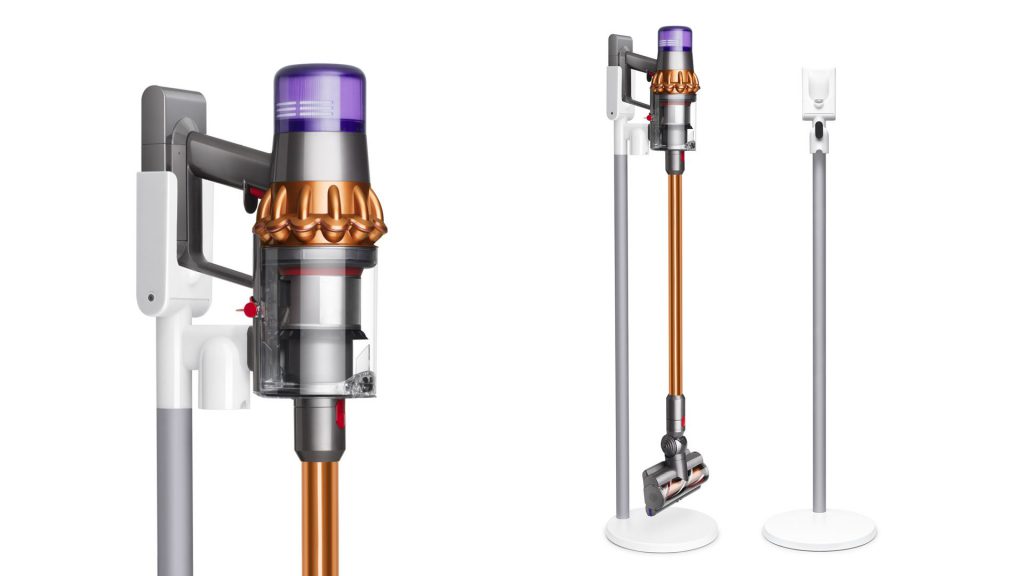
Short Description: My last project at Dyson where V11 accessory was needed that would fulfill many requirements from aesthetics to functionality through safety of usage. The product is pure in its look as per the requirements, has low footprint with optimized stability to meet safety regulations. It was a challenging project as for such product there was nearly everyone in the company who had different vision how this should look like and what it should do. Budget also was very challenging.
Result: Product in sale, designed to the spec and to the budged. Patent in force: Application Number: GB2019053464; Publication Number: 2020/136366
Tasks:
- Creating specification
- Creating risks lists
- CAD design/modelling
- Running CAD checks
- CAD drawings preparations (company standards based on BS88888)
- FEA simulation (Ansys)
- Thermal analysis for solids – FEA (Ansys)
- Hand calculations
- Tolerance stacking and tolerance risks documents generation
- Test methods writing
- Using standardized test methods to conduct testing
- Tool actions
- Moulding gate proposals
- Generating Tool forms
- Proposing tolling actions
- COSH for new materials
- Arduino usage and altering codes
- Creating sensors to test principles of sensors physics
- Proposing new tests (vision tracking, litmus paper in water ingress chcking, Digital Motors robustness tests in unknown environments)
- Material selection and research of the new ones
- Data collection and MSA – Measurement System Analysis
- DoE – Design of Experiment
- Measuring product performance
- Hypotesis Testing
- Liaising with international suppliers
- Selection of suppliers to deliver new manufacturing methods
- DFMEA creation
- Design to Manufacture
- Electric components, switches and their mechanisms design
- Prototyping selection (SLS, FDM, SLA, Vacuum Casting, Laser Cutting, Cardboard Modeling, Aluminium Extrusion)
- Test rigs and product rigs design and fabrication
- Data Management with PLM (Teamcenter)Full design cycle from a concept to a functional short run production prototypes
- Project management
- Suppliers selection and management of the selected ones
- Contractors selection and management
- 3D modeling for marketing purposes
- Documentation management
- Source and select components (pumps, fittings, sensors, structures)
Tools: NX, Ansys, Minitab, LabView, Teamcenter, Capra, MS Office, Matlab, Arduino, In-house software and hardware, for frequency measurement, power draw, pressure drops, leaks, EMC